120 Tons/hr
For a customer in California, we delivered an onion tail and grading line with a capacity of 120 tons per hour. The onions are graded directly from the field and stored in the cold stores. The onions are the large white American onions. Very soft with little skin. The onions must be graded very carefully. The onions are brought directly from the field into the line with side tipping wagons. The receiving is in long receiving hoppers. With these reception hoppers, the smallest possible drop height is achieved. The customer’s existing line had many technical shortcomings, which meant that the line often stood still. The explicit requirement of the customer was therefore a very reliable line. The clustommer doesn’t want to work with electronic sorters or optical graders. Over the past four years, more than ten thousand semi-loads have crossed the line to this day. In this period there has not yet been a technical defect and service and maintenance was minimal. Another strict condition was that the line had to have a good logistical routing. By setting up the sorters in line against each other, we have created a supply route in which two side tippers can feed the line at the same time without conflicting with each other. The line also had to be as clear and efficient as possible at the output. The graded onions of the two radial graders of sixty tons per hour each come next to each other. The starting point was and always is to keep the number of forklift movements to a minimum therefore we designed a automated box handling system. With the automatic box system, you always bring six boxes into the line and take out six boxes. The whole is equipped with an air extraction system from Meconaf.
The whole project had to be managed with an simple central system. Some things still need to be realized.
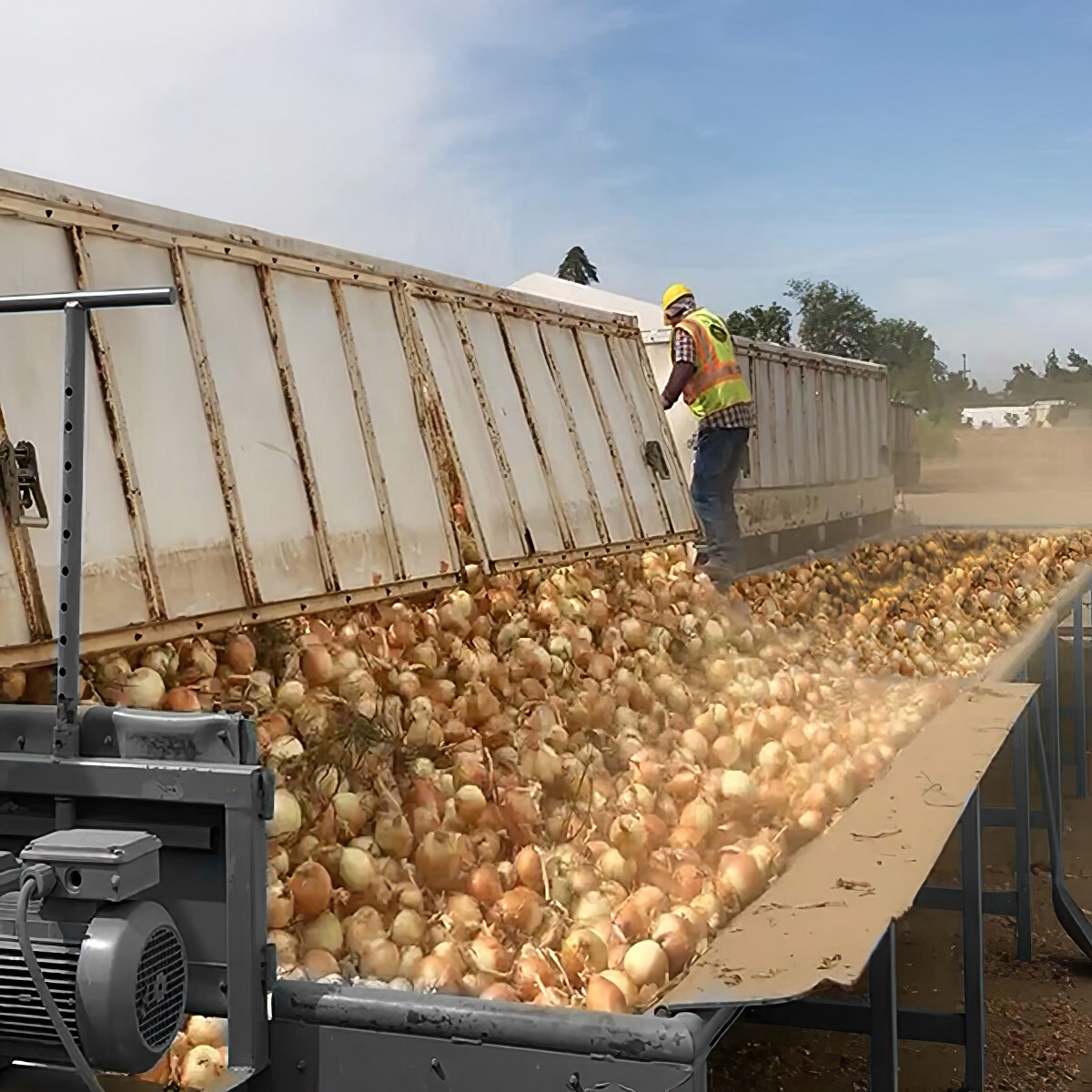
Zone 1 : Receiving area
The potatoes arrive in potato belt trucks. The trucks first have to cross the weighbridge. Here, in addition to the gross weight, the load factor that has been agreed is immediately recorded. For example, at least 27 tons. Under loading is charged to prevent unnecessary truck movements. At the reception there is room for two trucks, the second can be ready while the first is still unloading. The reception at the line is in a receiving hopper. The hopper has a large content and capacity but does not have an exceptionally heavy construction because the supply is with potato trucks. The price of this bunker is therefore favourable. After the receiving hopper the potatoes go to a destoner then to a skin separator. Here, old corn cobs and organic residues are removed. After destoning and skin separation, the potatoes come into a drum washer. After the washer, you can choose a polisher or a horizontal brushing machine. The choice depends on the type of potatoes, degree of contamination and skin quality. The washing part (Wet part) is separated from the sorting, grading and packing process. Water management is supported by a smart water recirculation system from Taneco. The Taneco purification system is very easy to install. The whole system is installed in a twenty foot container. We take care of the entire water management with drawings and calculations.
Zone 2 : Topping area’s
In zone two, the onions are topped and the dust extraction installation is placed. In order to achieve the capacity of 60 tons per hour per radial grader, we have put four onion toppers in a row here. After the receiving hoppers, the onions are first pre-graded with string graders in two sizes. The two sizes come on two different onion toppers. The onion toppers have different sizes of sieves. With pre-graded onions and two onion toppers you get an optimal topping effect. The onion toppers are equipped with so-called open top doors to simplify the changing of the sieves. At the topping part there are several dust extraction points. When onions are processed in the open air, it is a good idea to cover transport belts on the top. In this way you prevent a lot of spread of dust and skins on the company premises, and that of the neighbors. .
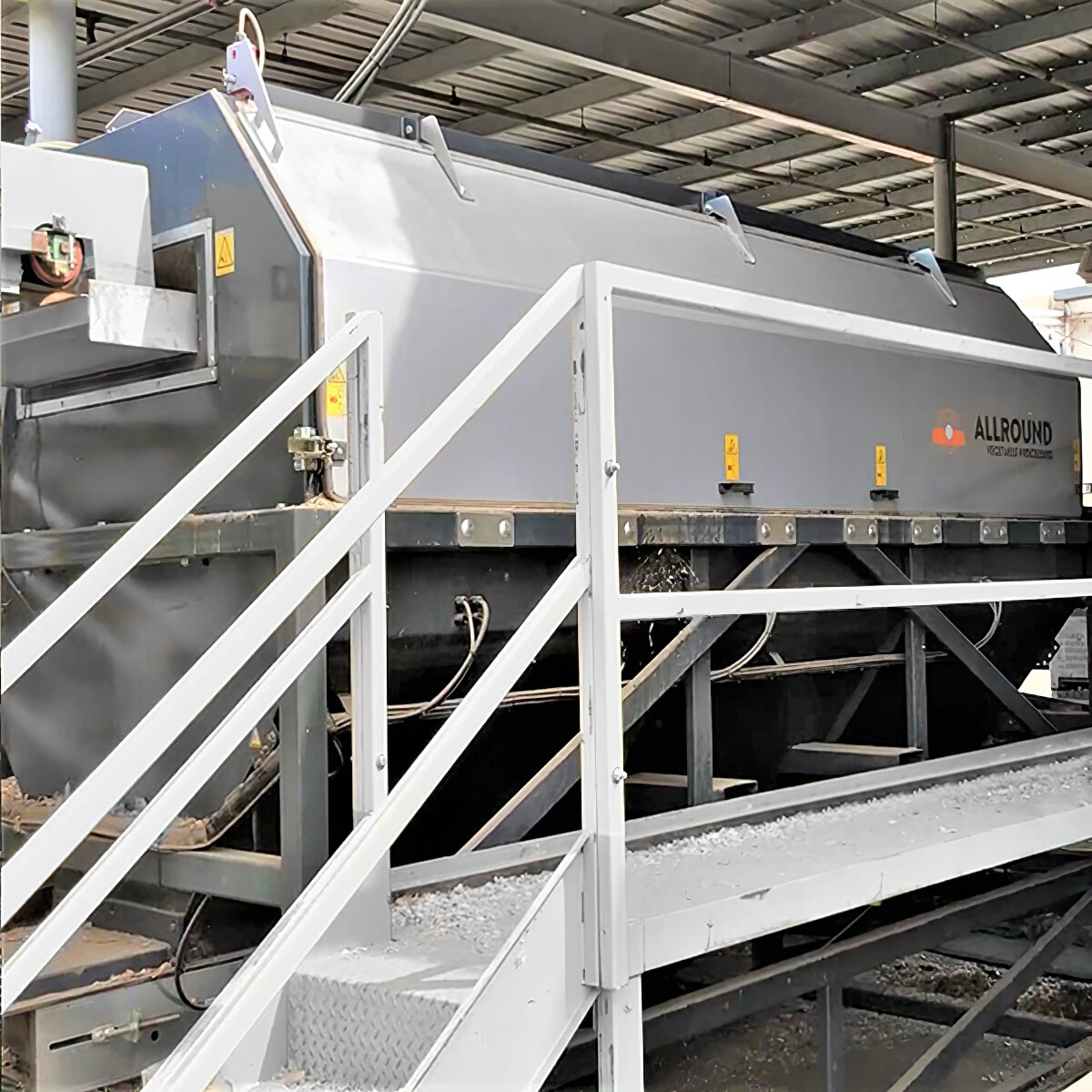
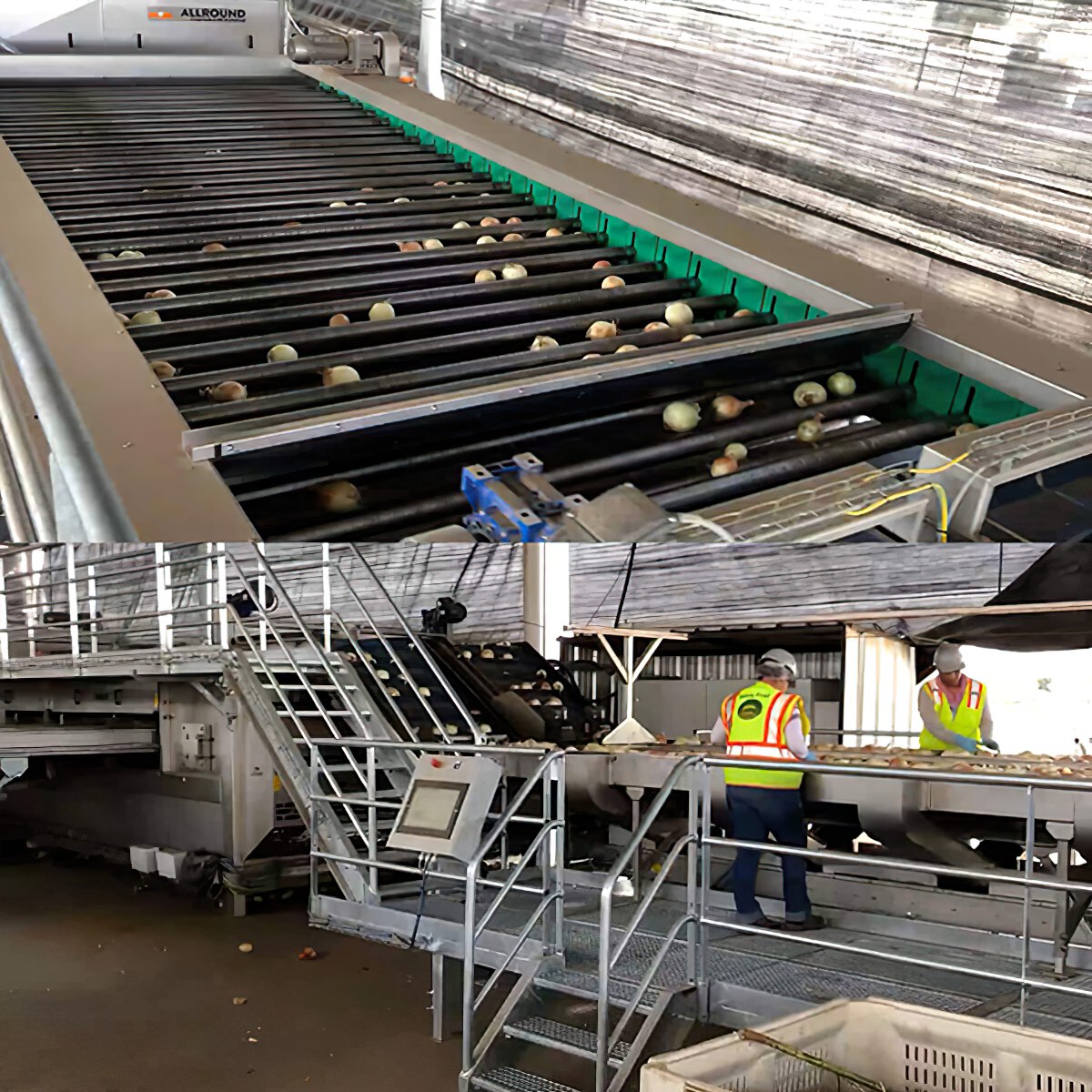
Zone 3 : Manual inspection and grading
In zone three the manual inspection and the grading is done. The onions from the output of the four onion toppers will be distributed by one collection belt to the manual inspection unit. The inspection unit is with a flat belt. For these sensitive onions it is not advisable to use a roller inspection table because this causes too much abrasive. The inspection unit has three transport belts. The middle belt is for the rejected onions. This middle bekt is lower than the two outer transport blets. By placing the transport belt for rejections in the middle and lower, the people work forward this increases productivity. The rejected onions are brought back to a box filling belt. At the selection unit there is room for twelve people. At normal quality considerable fewer people are needed. After the inspection unit, the onions are taken to the Radial grader with elevators. The elevators have a so-called swanneck to keep the drop height to a minimum. The Radial graders have a grading width of 260 cm. The machines are sold at a capacity of sixty tons per hour but in practice they reach eighty tons per grader. These machines are also often used as pre-graders in optical sorters. This gives the optical sorter a much higher capacity. The radial grader is a good final grader or pre-sorter for onions. Very reliable easy to use and last ot least very low maintenance costs.
Zone 4 : Box automation
Lorem Ipsum is simply dummy text of the printing and typesetting industry. Lorem Ipsum has been the industry’s standard dummy text ever since the 1500s, when an unknown printer took a galley of type and scrambled it to make a type specimen book. It has survived not only five centuries, but also the leap into electronic typesetting, remaining essentially unchanged. It was popularized in the 1960s with the release of Letraset sheets containing Lorem Ipsum passages, and more recently with desktop publishing software like Aldus PageMaker including versions of Lorem Ipsum. logistics process.
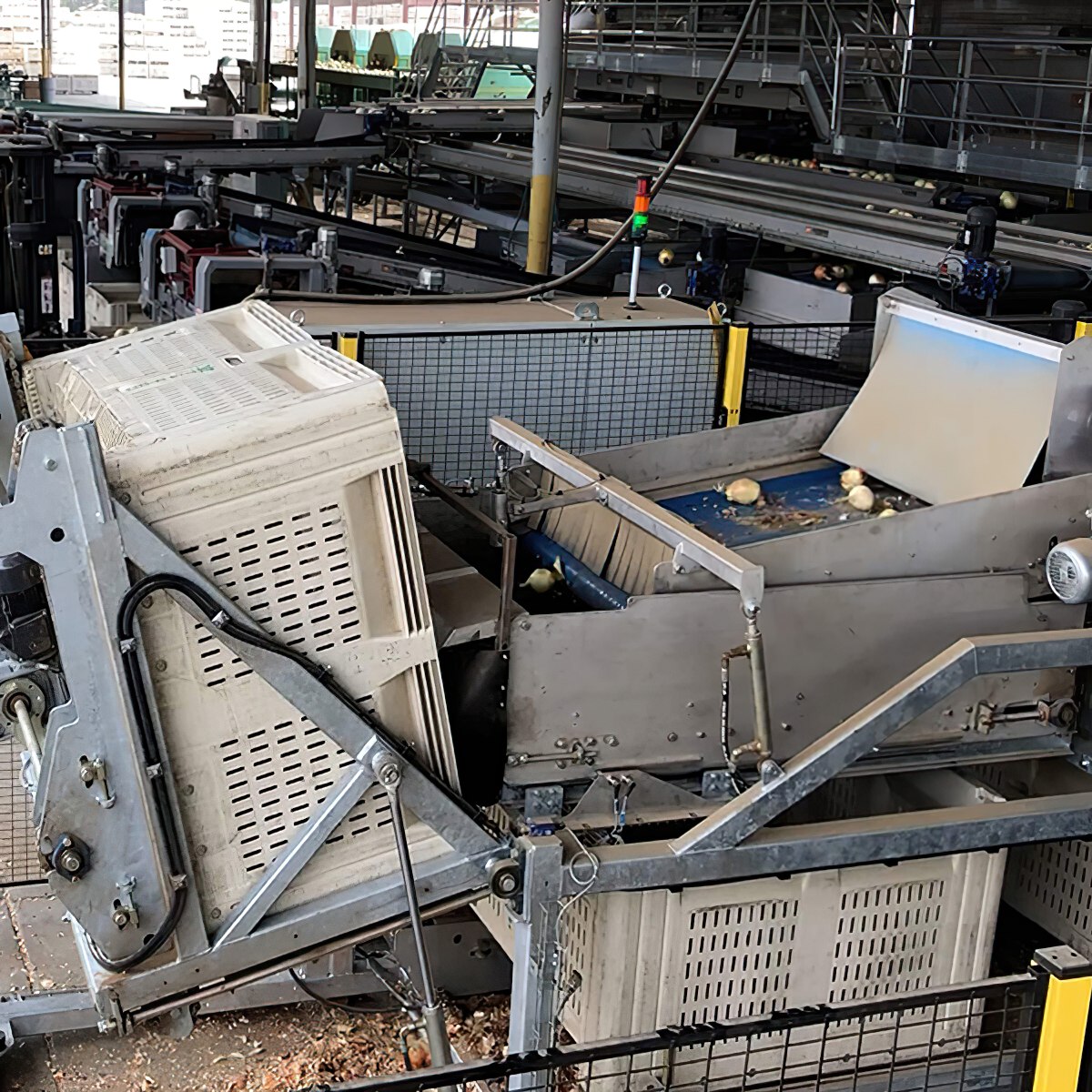