25 Tons/hr
F or a wholesaler in Canada, in six different products, we carried out a Greenfield project for a complete processing line. The company delivers to the premium fresh market every day. The line can handle multiple products but is purchased for: carrots, parsnips, beetroot, turnips and rutabages. With some adjustments, you could also process potatoes and onions over the line. We have reached a sorting range on the line from minimum 0.63 inches to a maximum of 9.8 inches. Between the minimum and the maximum size, each size can be set. The line has six grades. On the selector unit we have an opportunity to make positive selection to premium quality. The infeed of unwashed product and the washing section are located in a separate room.
The input with tip trailers is via a receiving hopper outside. The import of unwashed procunt with jumbo bags or cubic boxes is received via a receiving hopper. There is also a possibility to bring washed and quality controlled but unsorted product into the line. There is also a receiving hopper for sorting product to be brought to the packaging station of your choice. The polisher is placed after the manual inspection because there is then a choice whether or not to polish. We have the possibility to sort the product into six sizes. Two multi weighing and packaging stations in combination with a few manual packaging tables make this line extremely flexible. There are also large cold stores at the production. However, together with the customer, we have designed the building where the processing and shipping takes place as a docking distribution center. It is therefore not possible to carry out long-term storage in this place. The entire line is made of Stainless Steel. A beautiful project where we would like to inform you in detail in a personal interview via video conference.
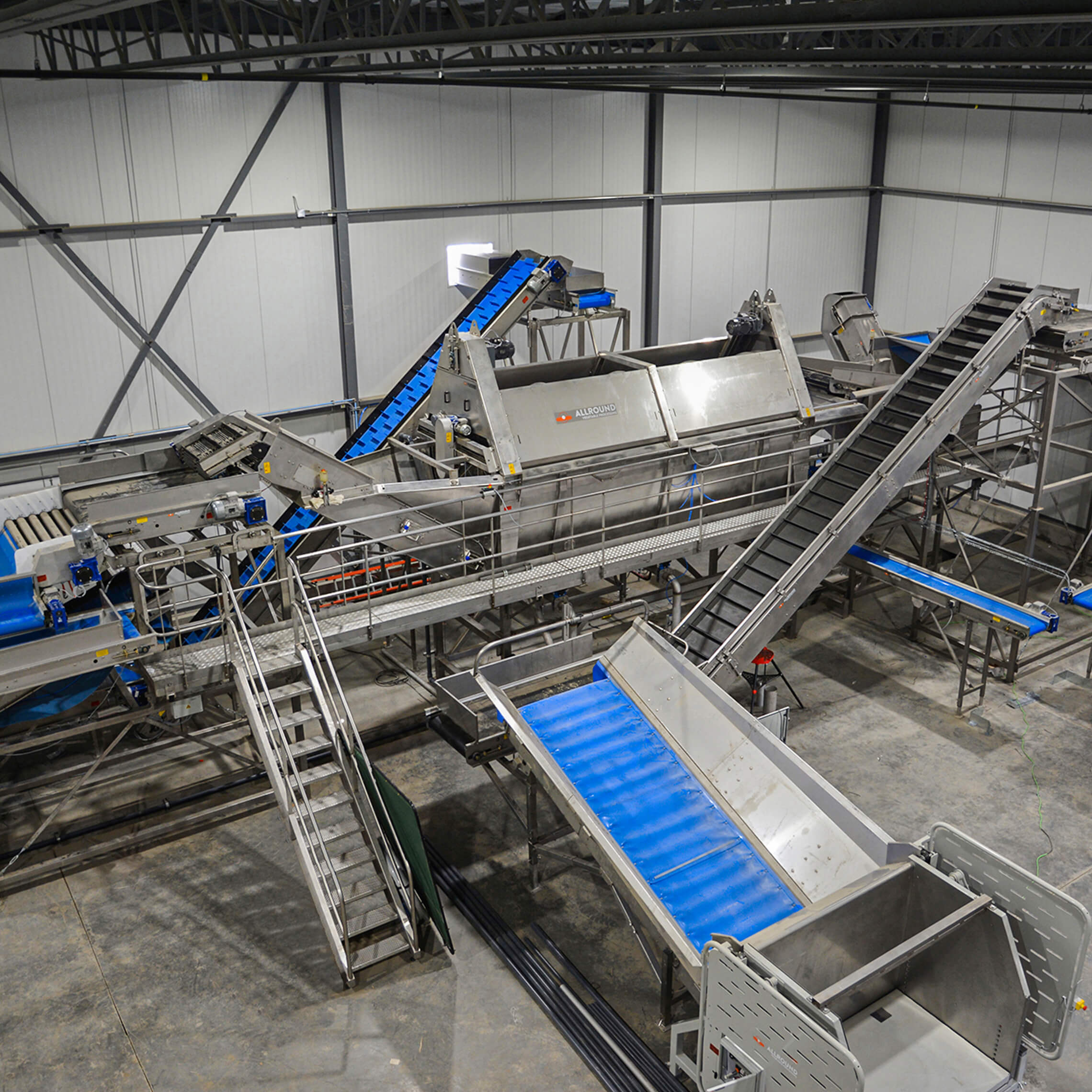
Zone 1 : Receiving and washing part
Zone 1 is the so-called dirty department. Here the unwashed product arrives via tip trailers or big bags or cubic boxes. The large hopper in the separate room is for the tip trailers. Product freshly harvested from the land is supplied here with tip trailers. The freshly harvested products are from our own cultivation. When designing the project, two refrigerated rooms were created for product from suppliers. These products can be supplied in jumbo bags and cubic boxes. The jumbo bags and cubic boxes can be unloaded and temporarily stored in this room. As mentioned earlier we have here a distribution center as a docking station. The product that comes in must be removed within a few days. The storage space for the cubic boxes and jumbo bags is only sufficient for a few days. The wash is divided into a destoner and a drum washer. After the drum washer is another adjustable roller set for waste or and undersize. After this roller set there is a choice for a chunk grader or directly to the manual selection unit. The chunk grader is used for carrots and parsnips.with drawings and calculations.
Zone 2 : Polishing, inspection, grading one
Here the products are fed over the selection unit. The selection unit is multi-functional. Here the rejected product can be placed in the middle. The selection unit is then used by default for so-called negative selection. However, the customer also wants to be able to manually remove a certain size or quality from the batch. We then speak of positive selection. We then get the very best out of the party instead of the rejected ones. After the selection unit you can choose to polish or to proceed directly to the first sorter. In zone two you can also bring washed and selected but not sorted product to the sorting line. In zone two is also the first sorting machine. We need an extra sorting machine here to reach the extreme minimum size and maximum size. The first size of this sorting machine is 4.3 inches going to the next sorting machine. The maximum size of this machine is 10.2 inches. The first size of the first sorter goes to sorter two the next two sizes are for the market. For example, rutabages, turnips, seleriac and beetroot.
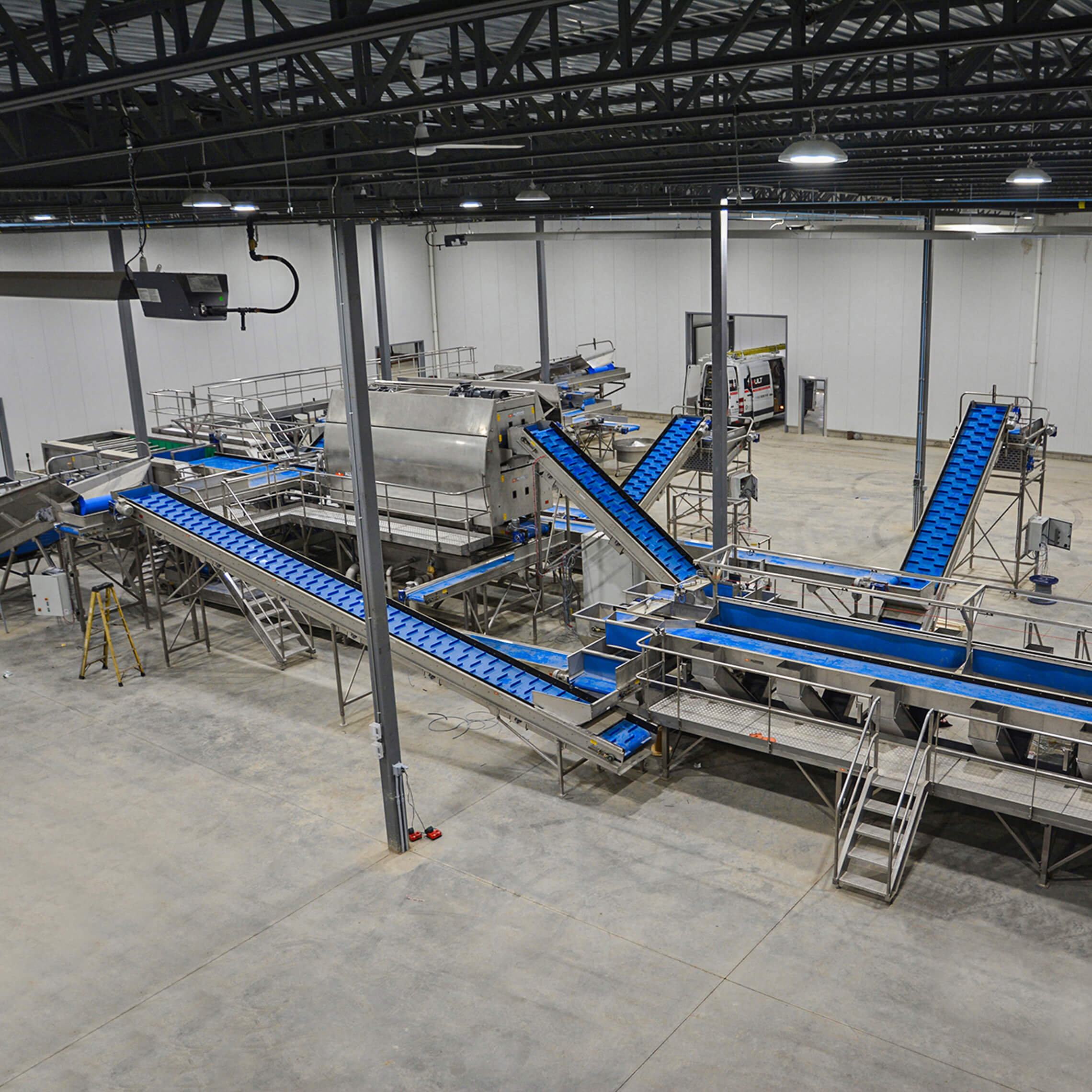
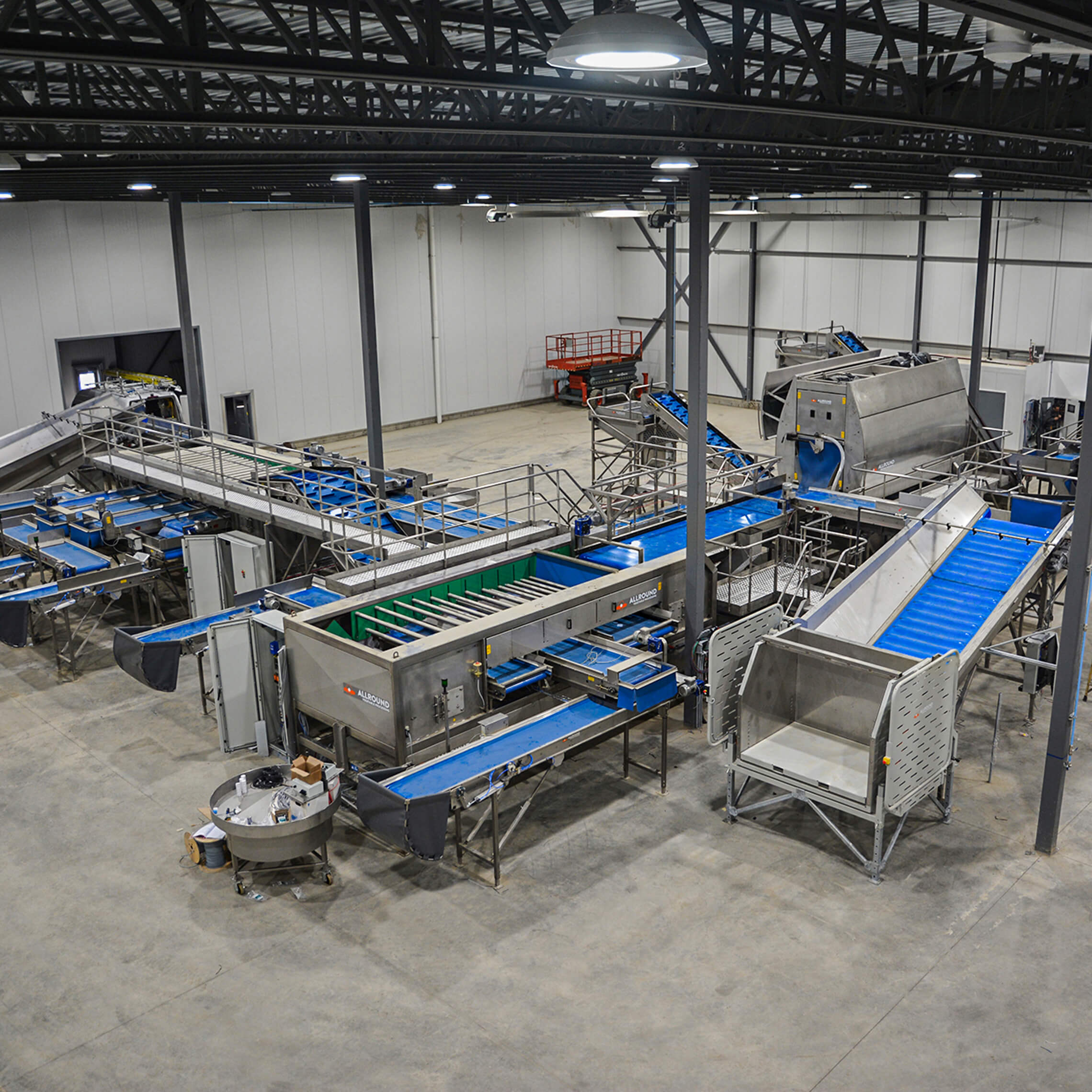
Zone 3 : Grading and manual packing
At zone three, the second grading machine has been installed. After this grading machine, we have a wide range of possibilities for the graded product. Each grade of the lift roller grader can be done to a cubic box for temporary storage. For three grades, three round packing tables have been placed for manual packing. At the sorting machine there is also a bunker where sorted and washed product can be distributed to one of the packaging machines. From the grading machine you can bring each grade to each of the two Upmann multi head weighers. This part of the line is where the actual distribution center of the line is situated. We have achieved maximum flexibility. The limitation is the number of automated weighers and packers.
Zone 4:
The distribution center is a logical system where the principle of first in first out is strictly applied. The production and shipping departments receive the orders from the sales department. The prepared orders are placed in a fixed system in the distribution center by the members of the production team. With the help of tablets, the orders and places in the distribution center are communicated to the employees of production. To support this, large electronic order screens are set up at the production location in the line. The same process takes place at dispatch. The employees receive the orders for dispatch on tablets. Large electronic screens are also set up at the dispatch department. Management by walking is a thing of the past. It is now a tightly organized logistics process.
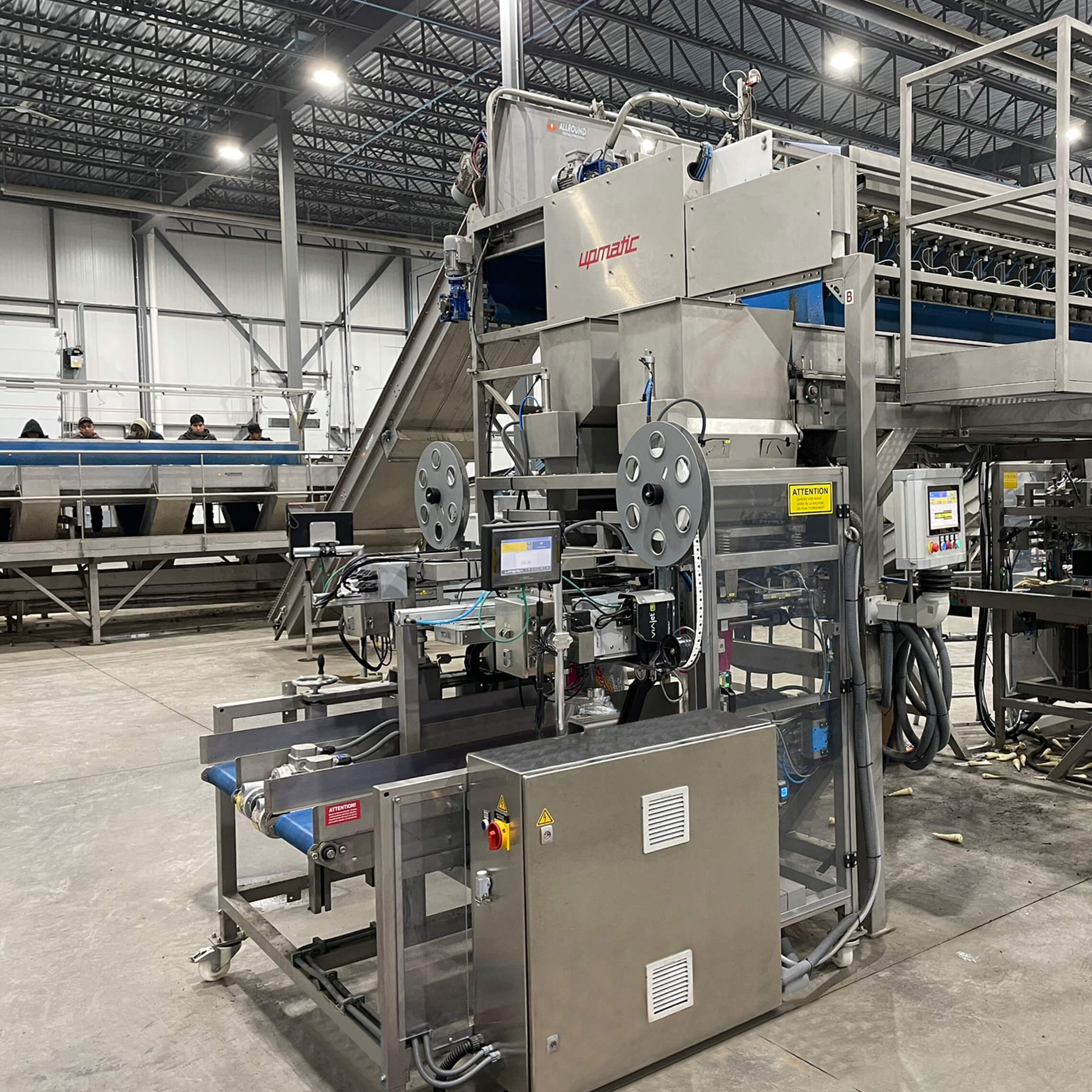