25 Tons/hr
A project to replace an existing multi product line. The new line had to be drawn in an existing building. Inevitably you have problems with doors, heights and electricity connections. In close consultation with the civil contractor, however, these are relatively easy to solve. A clear, unambiguous communication and evaluation is indispensable here. The entire processing of the produce, carrots, red beet and parsnips, had to be modernized. The company is a supplier to a wholesaler of carrots and carrot products and also supplies directly to distribution centers of a supermarket chain. The three crops are grown on a large scale on the farm. About five months a year, the produce are processed directly from the field and delivered daily. The collection of harvested produce for direct delivery is done in potato button belt trucks. The crops are also grown for storage. Throughout the year there is cooperation with suppliers. Both for freshly harvested crops and from storage. The customer was confronted by its customers with a strict new requirement. The carrots and parsnips must be delivered refrigerated per coming season. The only solution is a hydrocooler. A large hydro cooler is part of the project. The Allround hydrocooler is sold all over the world and functions super. The hydrocooler is bypassed when the carrots and parsnips are not needed to be cooled. Another area of great concern is the changing environmental requirements for the use of fresh water and the disposal of used water. We have proposed a completely new water management system. Water use is reduced by up to 95% through a very smart recirculation system. For the packaging and collection of the retail packaging, we have proposed a robotized system. This new system can collect trays and bags in different RPCs at the same time. The RPCs with trays and those with bags are both palletized with an IPLA palletizer and then collected and barcoded from the pallets. We have come up with a nice solution for processing, labor savings and environmental requirements.
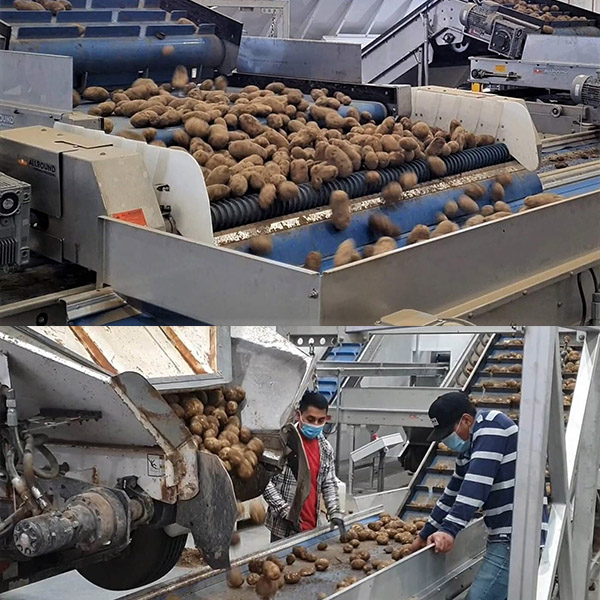
Zone 1 : Receiving and water cleaning
At the reception there is a a covered place for two trucks next to each other. In this way we avoid unnecessary waiting times. The installation works with a wet hopper so the potato button belt truck is used as a buffer upon receipt. The carrots come dirty from the field we have therefore used as much as possible flat transport belts so that they can be scraped off. In this way we prevent loose soil falling to the ground. To separate the loose soil from the carrots before washing, we installed a stand-alone finger roller test. In the same room we put the water treatment plant.
Taneco is specialized in Water treatment systems. Taneco offers specific solutions, based on customers demand and requirements and also offers plug and play systems. Customers as Aviko Potato, Mc Cain, AVEBE are using the Taneco systems already for years.
Taneco developed a solution for potato and vegetable processors to recycle wash water in a simple, compact and affordable way.
The system saves up to 95% on water.
The Agri WWT comes with capacities from 10 – 100 m3/h. The complete system is built in two 20ft containers and is fully tested in our factory and is fully installed within two working days.
We live in a world where water scarcity is increasing every day. In order for future generations to benefit from all the possibilities we have today, water is one of the most important resources that we must take care of. Our mission is to reduce the unnecessary use of water in such a way that companies use mainly their own recycled water. With this partnership we think we can reach our goal on making the world a little better.
Zone 2 : Pre washing, skin separation, washing and polishing
The soil where the carrots, beetroot and parsnips are grown is light but difficult to wash. We have divided the washing process into four parts. After the finger roll set, the product come in a wet hopper. Produce from the cold store are tipped directly into the wet hopper. At the transition from the wet hopper to the skin separator, a leaf separator is mounted. With freshly harvested product you often have a lot of leaves. In this area, many stem residues and corn cobs come with harvesting. We remove the stem residues and corn cobs with a skin separator. The waste from the leaf separator and the skin separator are collected on a belt and discharged outside. After the skin separator, the product enters a washer. The washer is a so-called dry washer. So there is no water level in the drum. The drum has a length of 15 feet with a diameter of four feet. After the washer is the possibility to go over the chunk grader to the polisher. This in case of carrots. The second option is to by- pass the chunk grader but go to the polisher. The third option is to by-pass both the chunk grader and the polisher.
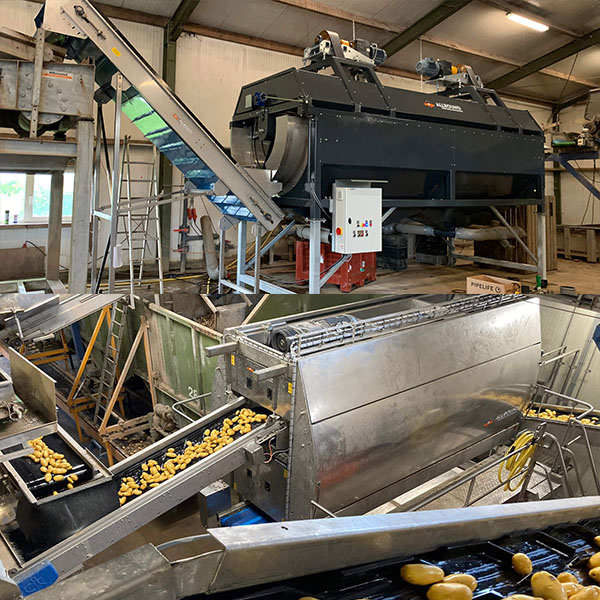
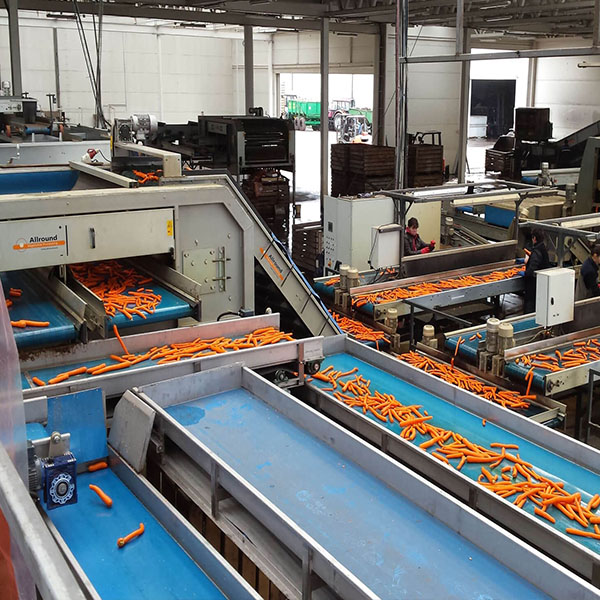
Zone 3 : Manual inspection, hydro cooling and grading
After washing, the product comes to the manul inspection. The name manual inspection is not complete. The company also grows and processes beetroot. Beetroot can grow very large when a number of seeds do not germinate. The size of this beetroot is then too large for the radial grader. The radial grader has a minimum size of 0,8 inch and a maximum size of 4,3 inch. We have a solution for this at the inspection table. At the inspection table you have two choices. You have the option to place rejected products on the middle belt. The second choice is to dispose of oversize in a chute mounted on the reading belt. The way to spread beetroot i.c. excess can also be automated. See here for project: multi product 25 tons. For budgetary reasons and because the acreage of beetroot is relatively small, we opted for the solution at the inspection unit. After the inspection unit, a choice can be made for the hydro cooler or a by pass. The hydro cooler is not against the wall but in the middle because you can then clean the machine more easily. The by pass is when you are not hydro cool. After the hydro cooler or by pass, the products come in an elevator to the radial grader. The elevator has a swanneck to minimize the drop height on the grading bed. The radial grader has four outlets. The size setting is automatic. Load cells in the outlet transport belts are available on request. With the help of the ze load cells you can see in real time what the grading schedule is. If desired, the system automatically adjusts its size setting. You can then adjust the settings to the
Zone 4:
Lorem ipsum dolor sit amet, consectetur adipiscing elit, sed do eiusmod tempor incididunt ut labore et dolore magna aliqua. Ut enim ad minim veniam, quis nostrud exercitation ullamco laboris nisi ut aliquip ex ea commodo consequat. Duis aute irure dolor in reprehenderit in voluptate velit esse cillum dolore eu fugiat nulla pariatur. Excepteur sint occaecat cupidatat non proident, sunt in culpa qui officia deserunt mollit anim id est laborum.
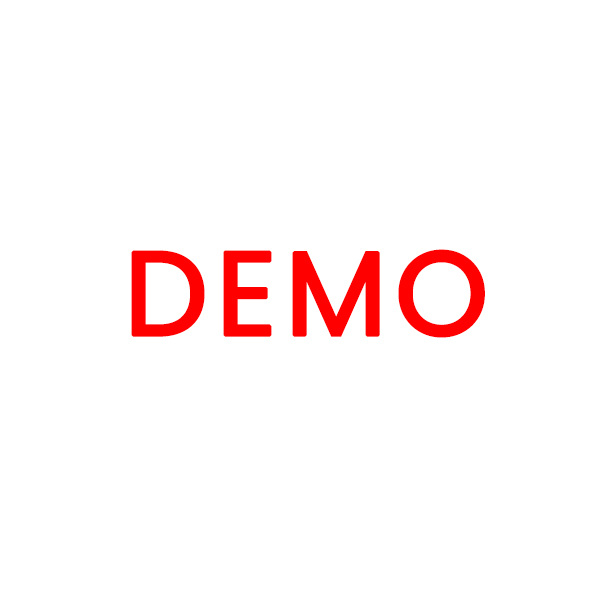