25 Tons/hr
The client’s wishes for this project were challenging. The line had to have maximum flexibility. Mechanical grading and electronic sorting/ grading had to work together seamlessly. When there are freshly harvested carrots or batches that are very healthy so no electronic sorting need to take place the carrots only go over the radial grade. However, when there are carrots that require a lot of inspection, there is the possibility to be graded by diameter by the radial grader. After this mechanical diameter grading the carrots go to the electronic sorters for quality sorting. After the electronic inspection and sorting, the carrots can still be returned for a final manual inspection. There is also the possibility to bring the electronic sorted carrots directly to the big bag / bin fillers. Manual inspection of any size of both the electronic sorters and radial sorters had to be done anywhere. Retail packaging is collected in RPCs (reusable plastic crates). For the palletization of these crates (RPCs) we used an IPLA crate palletizer. The carrots must be able to be collected both in cubic boxes or big bags and in retail packaging. This possibility should apply both to the carrots of the radial grader and those of the electronic sorters. The customer wanted to have a good overview of the entire line, so we made a platform from the beginning of the washing machine to the electronic sorters. The entire project had to be situated in a limited existing space. We have made more than twenty-five options together.
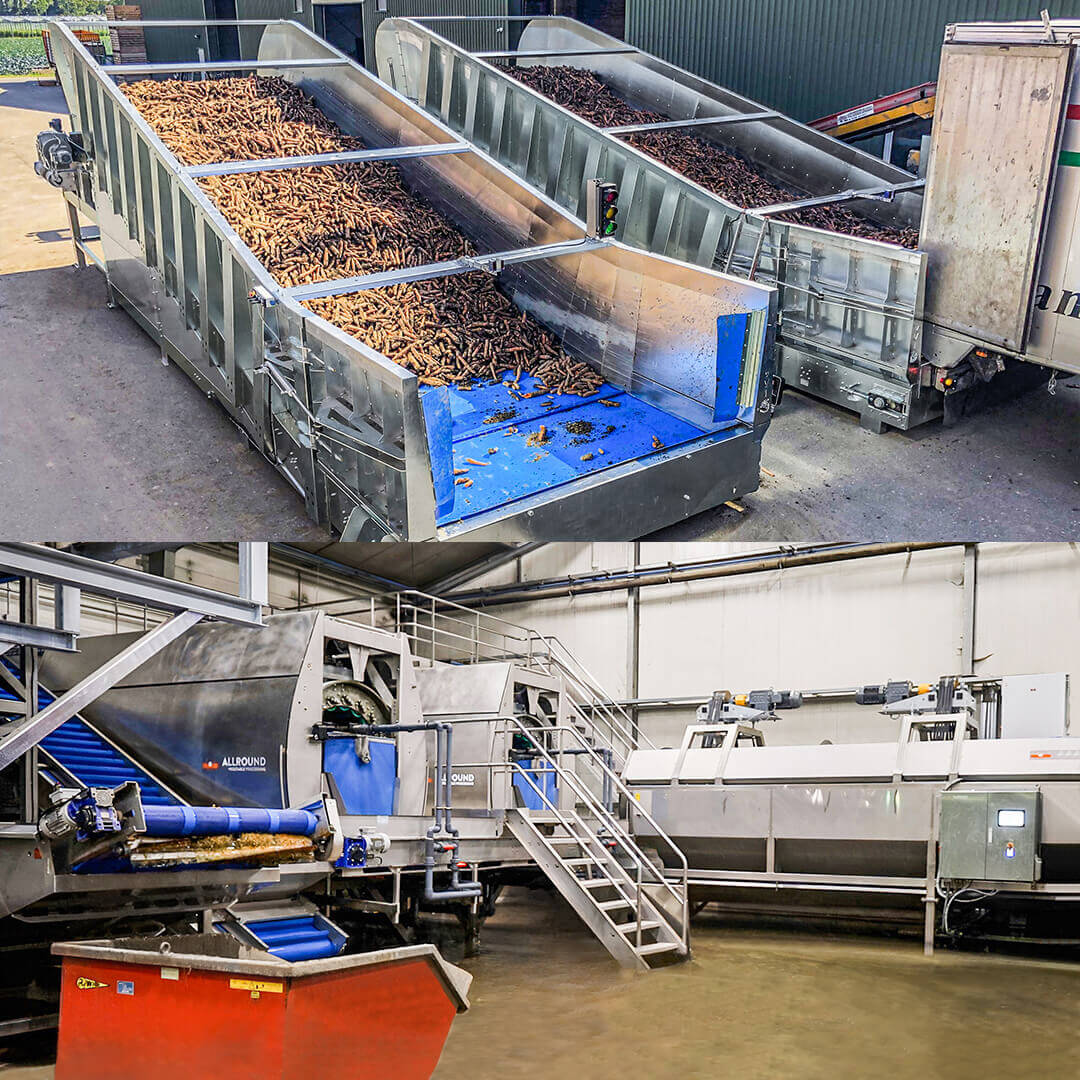
Zone 1 : Receiving and washing
The reception of the carrots for the line is located outside. The way of feeding the carrots to the line is with tip trailers and with cubic boxes. About five months a year, freshly harvested carrots are delivered with tip trailers. At the line we have put a large reception hopper. We want to limit the waiting time for the tip trailers as much as possible. A roller set has been installed at the hopper. The spiral roller set is to separate as much dry loose soil as possible. After the hopper, the carrots are taken to the washing machine with a trough belt. The input to the washing drum is with a water gutter. The washing machine has a drum of eight meters long with a diameter of 160 cm. The washing machine is especially for carrots so has no water level. In this way the carrots scrape each other clean. The output of the washing machine is with a perforated Intralox belt so we prevent water leaking onto the elevator. After the washing machine, there is the choice to run the carrots over the leaf separator or directly to the polishers.
Zone 2 : Polishing or no polishing
After the washing machine and or the leaf separator there is the choice to polish or to by pass the polishers. After the washer, the carrots come on a flat belt. From this band you can make the choice by slides on the band to bring the carrots to two polishers. If you do not want to polish, the carrots go directly to the evenflow hopper for the radial grader. To produce 25 tons to thirty tons per hour, we installed two TD 250 – 18. The polishers have eighteen rollers with a length of 350 cm. The polisher discharges on a central collection belt. After the polishers or after the by pass for the polishers, the carrots go to a large evenflow hopper. The evenflow hopper ensures an even supply of carrots on the radial grader. The more even the supply the better the grading. Under the leaf separator and the polishers a gutter is made. In the gutter, the organic waste from the leaf separator and that of the two polishers is collected. The organic waste is then taken to the sieve belt for the even flow where it is separated. Water will be brought back to the basins.
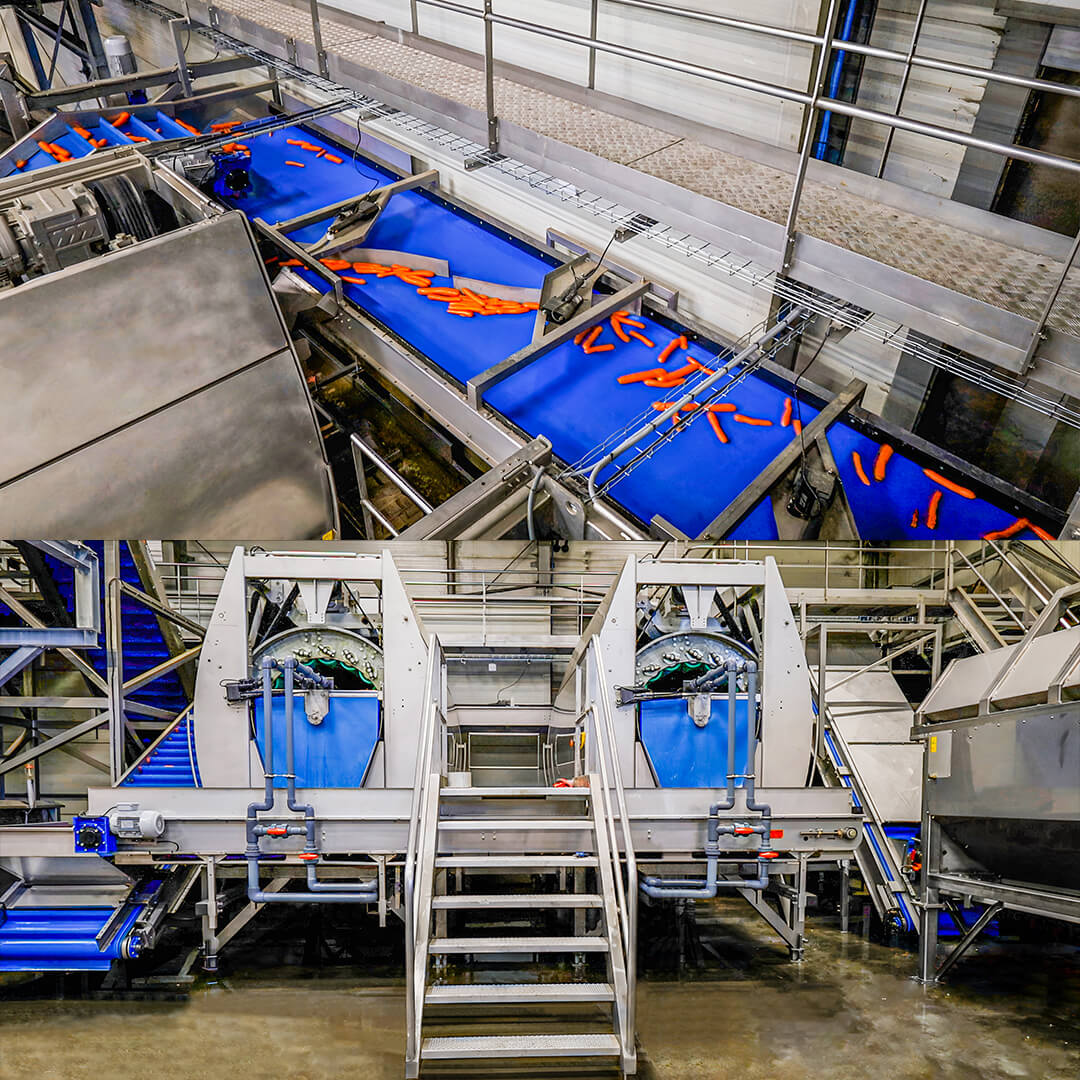
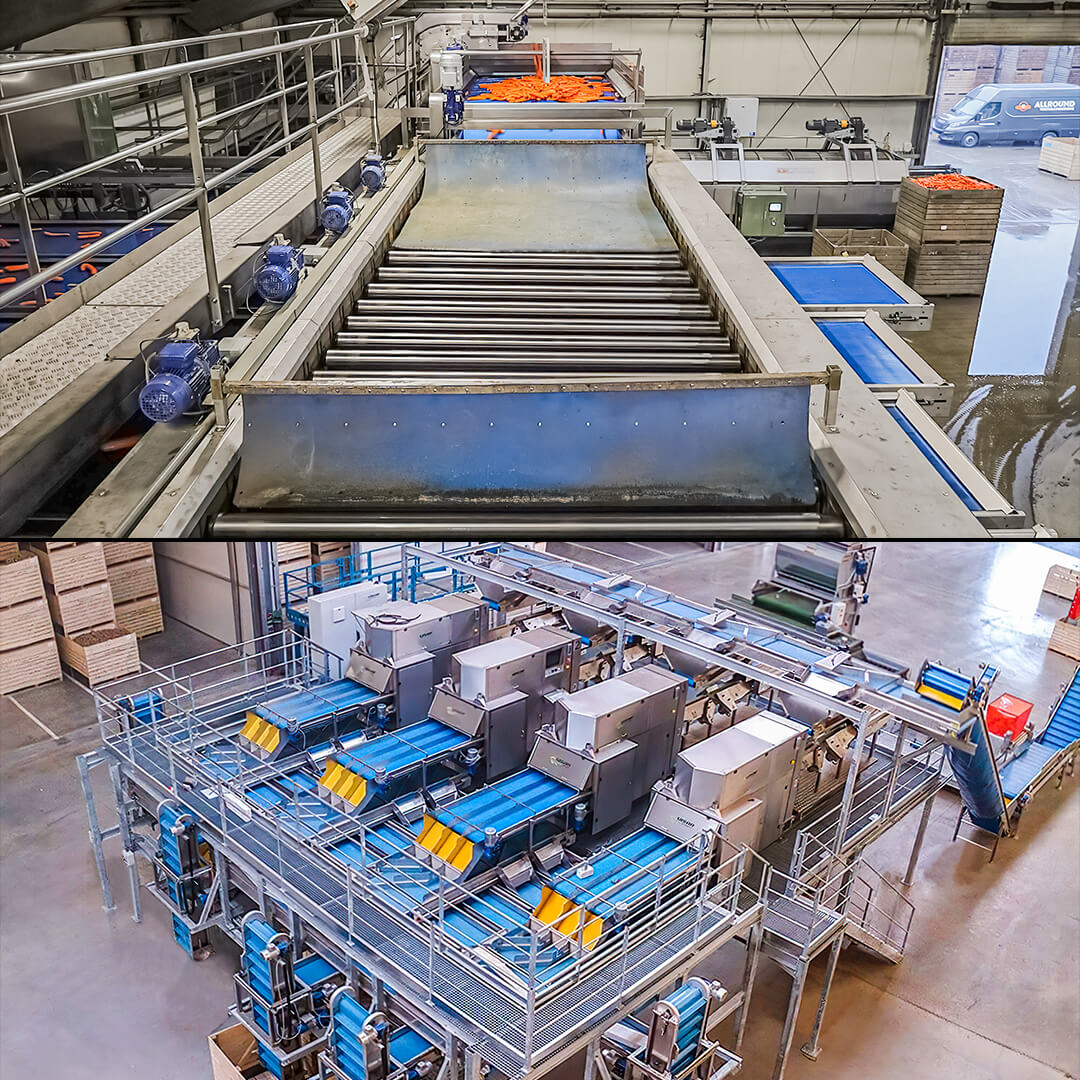
Zone 3 : Mechanical grading and electronic sorting
After the even flow, the carrots come on a supply belt to the radial grader. This infeed belt makes the supply even more regular in order to further optimize the radial grader. The radial grader has five output belts. All output are from Central Control Panel or tablet movable. It is possible to fill cubic boxes directly from the radial grader. For final manual inspection or supply to the electronic sorters, the carrots are placed on a distribution belt. The distribution belt has a length of sixty-seven feet and width of eight feet. The band is divided into four lanes. From the radial grader you can reach any lane. Each lane can go to any manual inspection table. Each lane on the distribution belt can go to the two electronic sorters. To be able to make this choice, electric pneumatic valves have been fitted to the distribution belt. From the electronic sorters you can make four qualities. You can go directly to the packers from here. The elevator and band to the packers is not shown on the drawing. The carrots which are not packed directly are collected in bins or big bags.
Zone 4
Omdat er snel moet worden geopereerd komen daardoor vrije zones, gericht op ontwikkeling, onder druk te staan.11 Een diepgaande discussie over een artistieke ontwikkeling, een serieus publiek debat over een kunstwerk of een grondig essay over een oeuvre wordt bijzaak, want tijdverlies
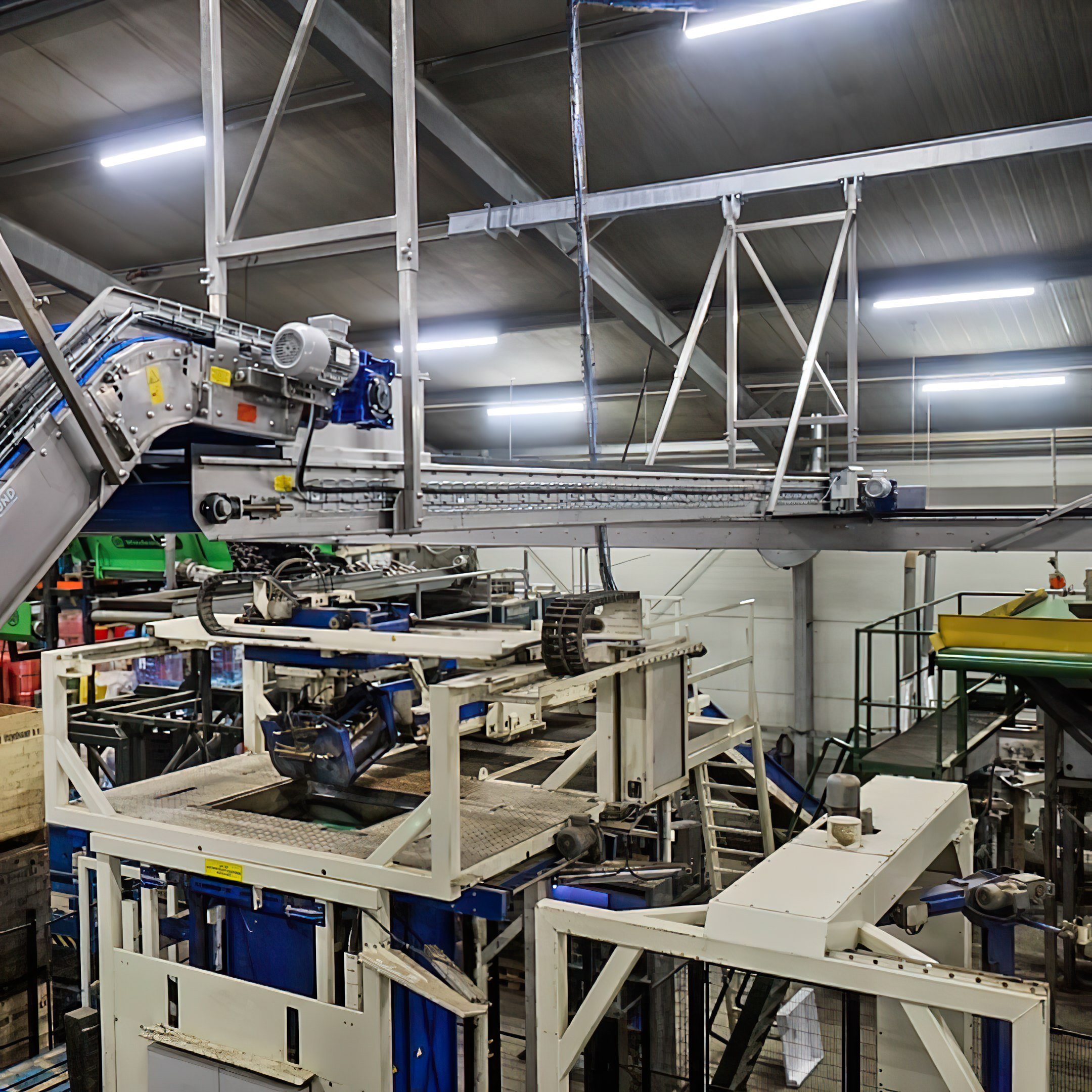