60 Tons/hr
The installation in the USA has a capacity of 60 tons. Five members of the Partnership of Companies are involved in this project. We have made thirty options. The processing process with the previous configuration of machines was very labor-intensive. They worked with two optical graders. Now with a large optical grader with a capacity of 60 tons per hour. Working with an optical grader gives great logistical advantages. We have been able to reduce the number of fork lifters by at least twenty. We have strictly adhered to our principle to collect the products once in the line only with special sizes or qualities in Macron’s. More than ninety percent goes directly into the final packaging. The onions collected in Macron’s are so small in volume that it is not profitable to connect special weighing and packaging machines to them. The plant also has a stand-alone weighing and packaging line for packaging where three colours of onions are packed into a package. The installation has a central dust and peel extraction system. The onions that are processed on the installation are topped by hand during harvesting. We have worked out another option with four onion toppers with by pass.
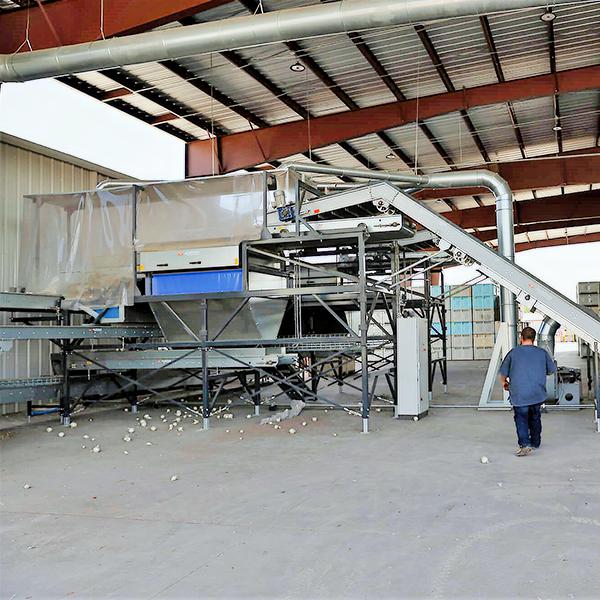
Zone 1
1. Box automation for supply of unprocessed onions. With this installation, six boxes are put in the supply at once. At a time, two boxes are emptied into the even flow. This way of emptying with the box automation of VHM we achieve a very large reduction of forklift movements. With this box automation, a very good routing / logistics of the full Macro bins and empty Macro bins can also be achieved.
2. Two brush machines next to each other. Possibility to by pass the brush machines. Combination with string grader for first pre-grading for Boilers and pre-pack.
3. Second Pre-grading. Separation of boilers and pre-pack.
4. Central waste collection. All waste from the line and the dust extraction installation, from the brush machines at the beginning to the reading places for the packaging machines, are eventually collected on a conveyor belt. The collected waste is evenly filled in a truck. Maconaf installed 1 cyclo jet and 1 cyclone in this installation.
5. Dust extraction. This installation from Meconaf separates and removes the substance and peels from the onions at all critical points in the line. We start with the input / even flow bunker at the box automation, brush, and pre-sorting.
6. Possibility of manual preselection.
Zone 2
1. Evenflow hopper for an even supply to the optical grader.
2. Optical grader eight lanes. Capacity sixty tons per hour. Machine raised to height so that it can feed to Smart Hoppers. Optical sorter equipped with dust extraction Meconaf.
3. Outfeed of optical grader with vertical filling belts with box fillers for collosal, #2. Also a outfeed with box filler when one of the Allround Smart Hoppers is full. Possibility of supplying product to any weighing and packaging machine.
4. Allround Smart Hoppers for even flow between optical grader and weighing packing stations. Allround Smart Hoppers for gentle handling of more fragile products. Almost no drop heights. Almost all Allround Smart hoppers can direct product to all weighing and packing machines with an intelligent system of conveyor belts.
5. fragile products. Almost no drop heights. Almost all Allround Smart hoppers can direct product to all weighing and packing machines with an intelligent system of conveyor belts.
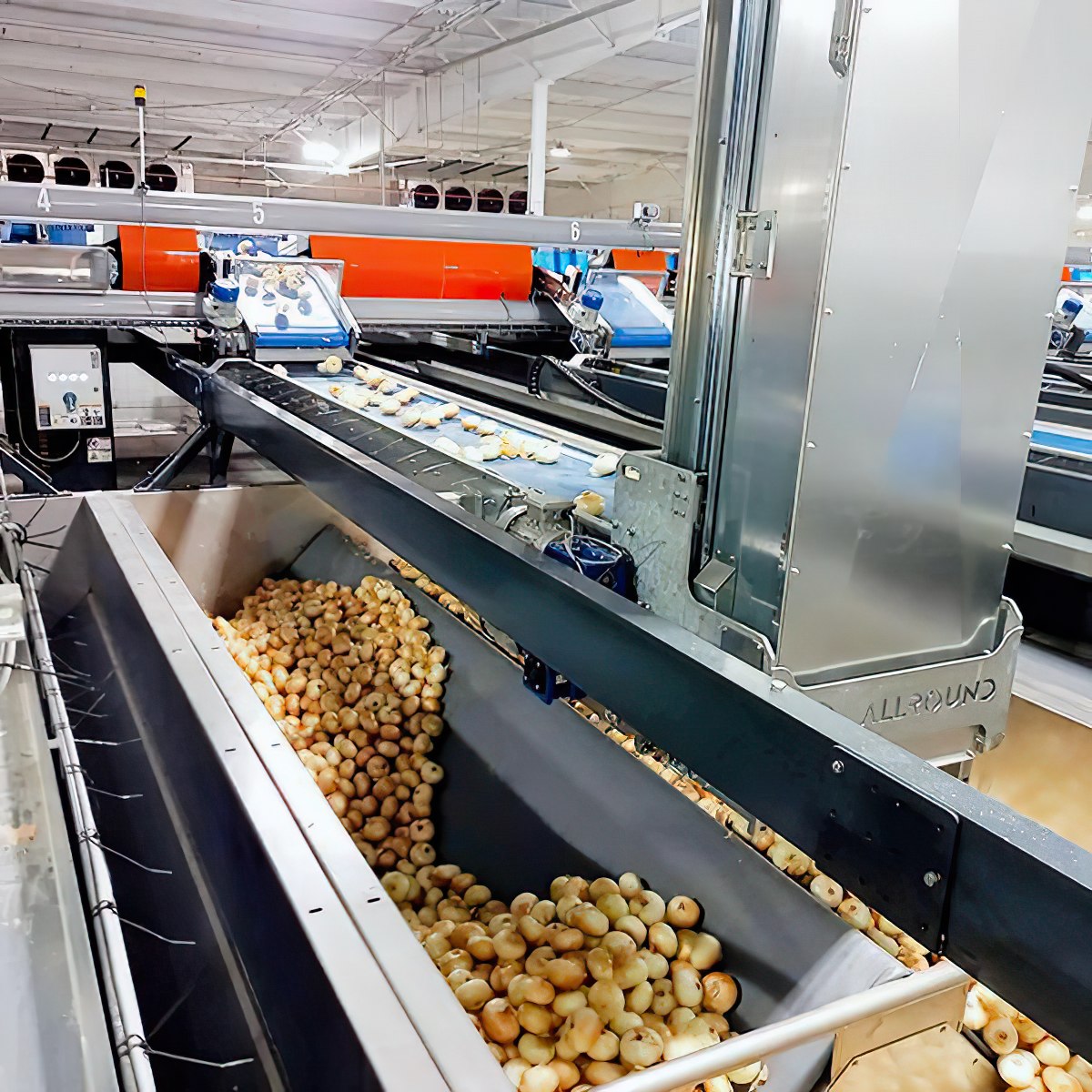
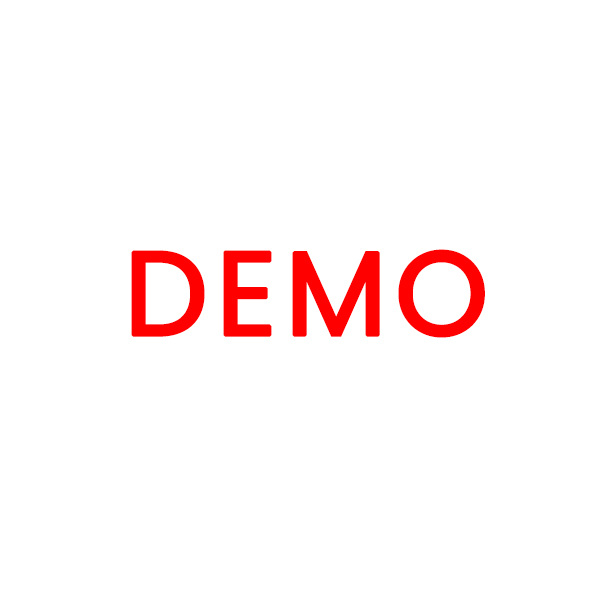
Zone 3
Weighing and packaging machines.
1. Stand alone weighing and packing station to pack three different colors of onions in one package.
2. Two high capacity weighing and packaging stations. Capacity up to 37 tons per hour.
3. Three weighing and packing stations for 1 kg to 5 kg.
Zone 4
Three IPLA palletizers for RPCs and cartons. These palletizers are the size to palletize a weighing and packaging bag. Machines are inexpensive to purchase, have a small footprint, are easy to operate.
Stand a;loen weigh and pack line to pack three different colors of onions in one package at the same time. Add to the weighing and packaging zone ne palletizing.
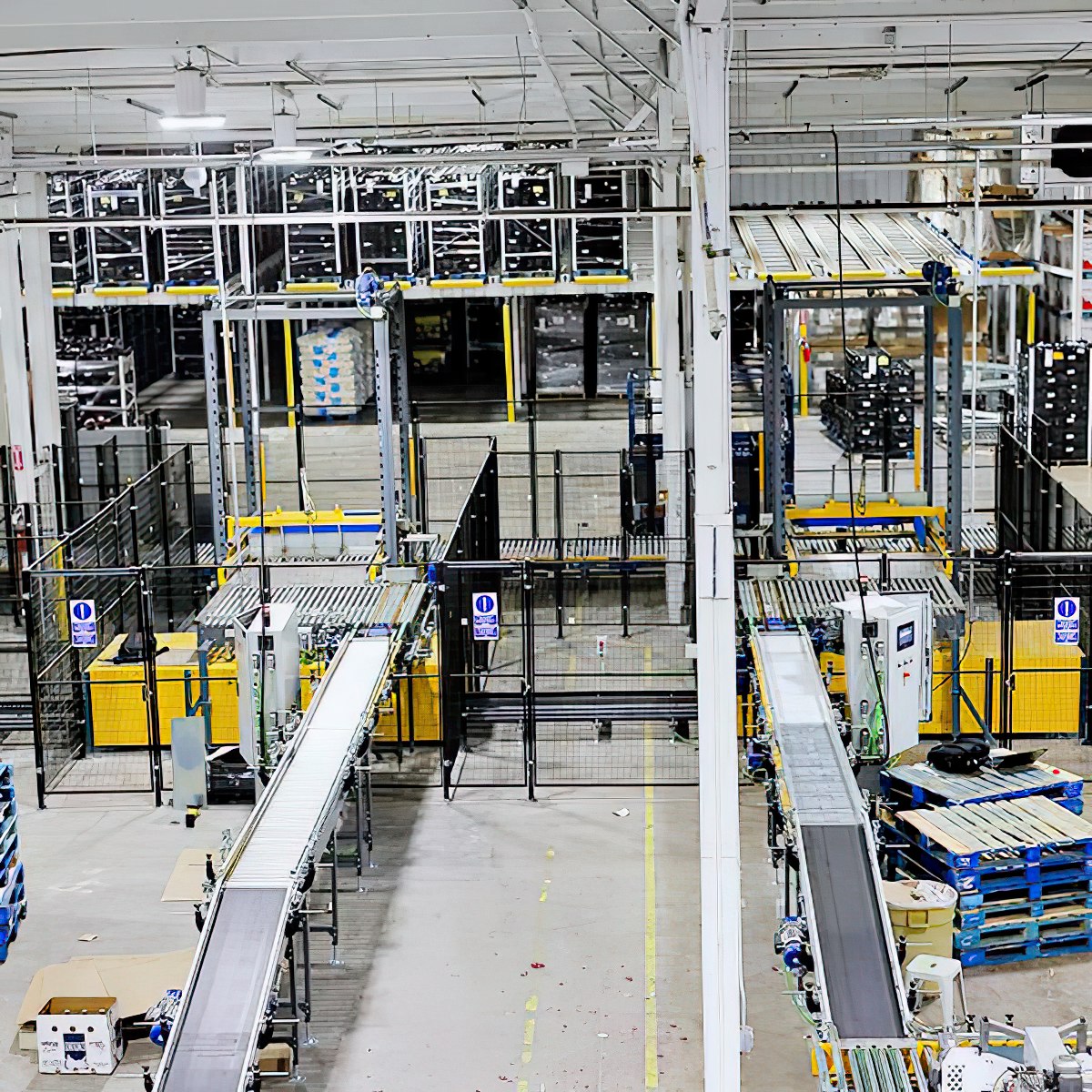